Where Should My New Distribution Center Be Located?
Jose Bejarano | 22 April 2016
Planning your next distribution center shouldn't be guesswork. Here are some recommendations for selecting the best location.
Whether you are looking to build your first distribution center (D.C.) or your fifth, the location of the D.C. is critical for the success of your operations. There are many factors that can affect the decision of where the facility should be, including: real estate cost, transportation cost, labor cost, access to quality labor, taxes, transportation routes, service level guarantees and many others. All of these factors might have different levels of importance depending on your overall supply chain strategy, but it is always good to keep each of them in mind throughout your entire decision-making process.
Transportation Cost
Transportation cost is typically one of the most important factors when deciding where to place a new facility as it could be a large source of cost, and it will continue to affect the bottom line of the company for as long as the facility exists. A common way to reduce transportation cost is to reduce the distance between the new D.C. and the customers you will be shipping to, while also minimizing the distance between the D.C. and the suppliers from whom you will be receiving product. Meaning that if most of my shipments go out to the Northeast, I would want to be as close as possible to my clients but close enough to my suppliers in the Midwest to avoid additional transportation cost.
Transportation Routes and Service Levels
Transportation routes go hand in hand with transportation cost as good transportation routes tend to imply lower cost, especially for less than truck loads and full truck load shipments. Additionally, the service level that transportation providers can give you based on the location of your facility can provide a strategic advantage worth considering. For example, a company that ships most of its product via parcel services might consider placing a D.C. close to an important parcel hub like Louisville, KY (UPS) or Memphis, TN (FedEx). Proximity to a parcel hub can provide better transportation rates and later pick-up times, which provides the ability to receive orders later and potentially complete more of them the same day.
Real Estate Cost and Taxes
Similar to when you are buying a house, the cost of real estate for distribution operations is highly dependent on the location, and it is important to find a balance between low cost and a good location. Additionally, some locations might offer tax advantages worth exploring that can help reduce the operating cost of a D.C. Not long ago we helped a client consolidate their supply chain network and learned that they would enjoy a tax benefit for international shipments coming out of certain locations. This ultimately became an important factor for their decision-making process.
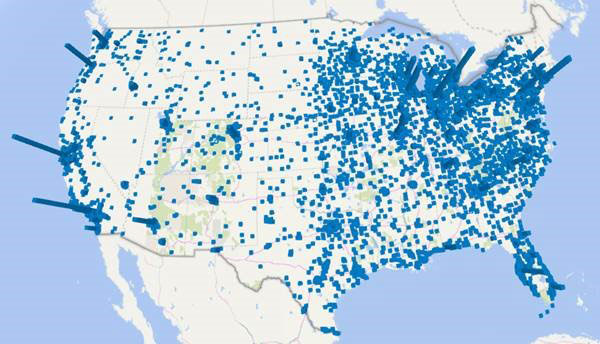
With so many factors to consider, determining the best location for a new facility requires a methodical and systematic analysis that can help balance all the important factors and achieve your supply chain strategy goals. This analysis is often referred to as supply chain optimization analysis, which is a study during which one would use mathematical optimization techniques to determine the optimal location for the new facility. This is often a very complex analysis, and real applications typically require the use of specialized software to determine the optimal solution. It is also advisable to consult with supply chain experts that can help you meet your supply chain goals and help you determine where your next distribution center should be located.
As Manager of International Sales, Jose works with Bastian international offices in Canada, Mexico, Brazil and India. Previously, in consulting, he worked with clients to evaluate their needs and operations in order to recommend solutions that help them increasing throughputs, productivity, and capacity. Jose leverages his extensive data analysis and modeling skills to glean insights from customer data to help drive fact-based concepts and designs. He has participated in projects across industries including medical devices, pharmaceuticals, apparel, and consumer goods. His projects include large green field DC designs, existing site retrofits, process improving and distribution network design and optimization.
Comments
No comments have been posted to this Blog Post
Leave a Reply
Your email address will not be published.
Comment
Thank you for your comment.