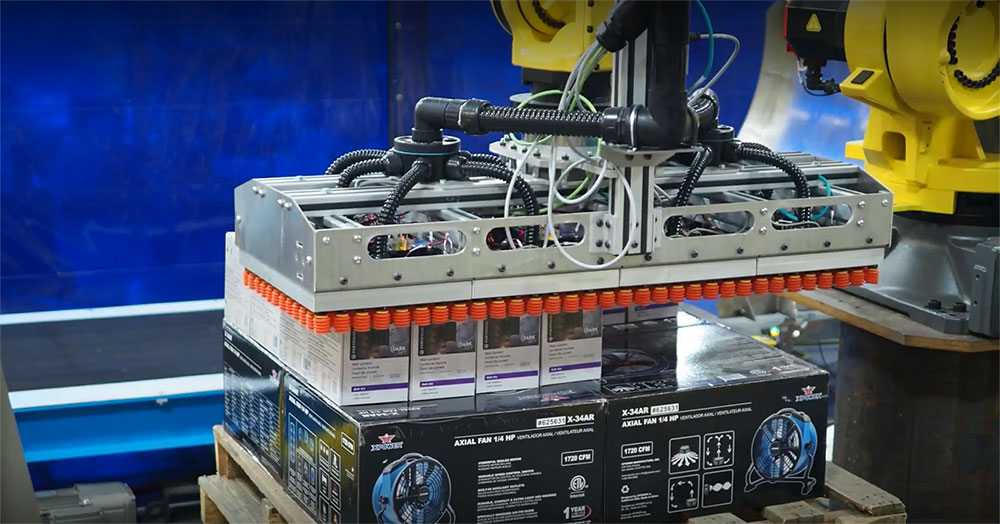
Considering Robotic Depalletizing? Evaluate These 3 Key Factors First
Trent Wideman | 20 March 2024
Does your facility have labor intensive, ergonomically challenging or repetitive operations that involve breaking down a pallet load? If so, robotic depalletizing could be a solution to help eliminate ergonomic strain, lower operating costs and allow for the reallocation of labor to other tasks within your facility.
Robotic depalletizing applications can take many forms, however, some common opportunities include breaking down a pallet of product from a supplier, feeding consumables to a production line and feeding product to other value add operations such as case labeling or decanting.
To select the appropriate technology for your operation’s needs, it’s important to evaluate the requirements and ROI of these potential systems.
A 3P Process to Depalletizing
To fully understand the scope of your potential depalletizing solution, consider the three key factors:
- Product
- Pallet Load
- Process
Product
The first data point to be evaluated is the type of product(s) that needs to be handled by the robotic depalletizing system. Ultimately, this drives the EoAT (end of arm tool) design or how the robotic system handles the product.
Corrugate cases are often handled with top vacuum that creates a seal on the top surface of the case to remove it from the pallet. These top vacuum EoATs can be sized to pick a single case at a time all the way up to picking a full layer of product at a time. Depending on the density, size and quality of the corrugate case, other picking mediums can be added to the EoAT to secure the product such as bottom support or side compression.
While corrugate cases are frequently processed in robotic depalletizing systems, there are many other products or container types that can be handled. From tires, to totes and steel wall panels, EoATs can be designed, built and integrated to handle less common products.
Understanding the type, size and range of products being handled upfront allows for the proper picking method to be selected so the system reliability and effectiveness can be maximized.
Pallet Load
The next data point to understand is the make up of the pallet load. The pallet load configuration drives several factors within a robotic system, with the largest item being the throughputs that a robotic cell can process.
For corrugate cases, there are typically three main pallet load configurations:
- Single case size or single SKU pallets
- Rainbow pallets - all cases of a particular layer are homogenous
- Completely mixed pallets
While all three configurations can be depalletized utilizing a full layer EoAT, it is most common for single SKU & rainbow pallets to be processed using this style of EoAT. Depalletizing a layer at a time maximizes the throughput of cases that come out of the robot cell as greater quantities of cases are picked with each robot cycle.
For mixed case pallets, typically an overhead vision system is paired with a top vacuum style single case pick EoAT. The vision system guides the robot through the depalletizing process by identifying the topmost/highest confidence pick target for the robot to retrieve.
Another consideration to recognize is the dunnage that exists on the pallet. Pallet loads often contain slip sheets throughout the load and/or has a stretch wrap applied to contain the outer edges of the load.
Robotic depalletizing cells can be paired with a de-wrap station upstream of the robot cell to remove the stretch film from the load. Slip sheets, however, can be processed by the robotic depalletizing system without operator intervention. Slip sheets, regardless of location (top sheet, layer/tier sheet or bottom sheet), can be identified by a vision system, removed by the robot and placed to a dunnage location in the cell that can be periodically removed.
Process
The final data point to consider is the process. This refers to what needs to happen with the product once it’s been depalletized.
Commonly, robotic depalletizing cells place cases to some form of outfeed conveyor. Unsurprisingly, this conveyor can take many forms. Full layer EoAT applications typically feed a “descrambler” which is a series of activated roller belted conveyors running at various speeds to orient all cases narrow side leading and in a single file flow. This allows for a manageable flow of cases to the downstream process.
Another common practice for depalletizing is product labeling, scanning and sorting. It’s imperative to partner with an experienced integrator well experienced in conveyance and sortation technologies that can provide an end-to-end solution for your facility.
A Fully Integrated Automated Warehouse
Leveraging decades of experience in various industries, Bastian Solutions can help you optimize not only pallet handling operations but many other functions such as fulfillment, shipping and storage, just to name a few. Our experts can help you select the right material handling equipment, implement the appropriate intralogistics software and optimize your processes for your business needs.
If you have an application you think is good a fit for robotic depalletizing, contact our engineers today and discuss how we can help you accomplish your goals!
Trent is a field application engineer with the robotics group of Bastian Solutions in St. Louis, MO. He has a Bachelor of Science degree in Industrial & Manufacturing Systems Engineering from the University of Missouri – Columbia. As a field application engineer, his duties include working with clients to determine their material handling needs and developing layouts for robotic systems.
Comments
No comments have been posted to this Blog Post
Leave a Reply
Your email address will not be published.
Comment
Thank you for your comment.