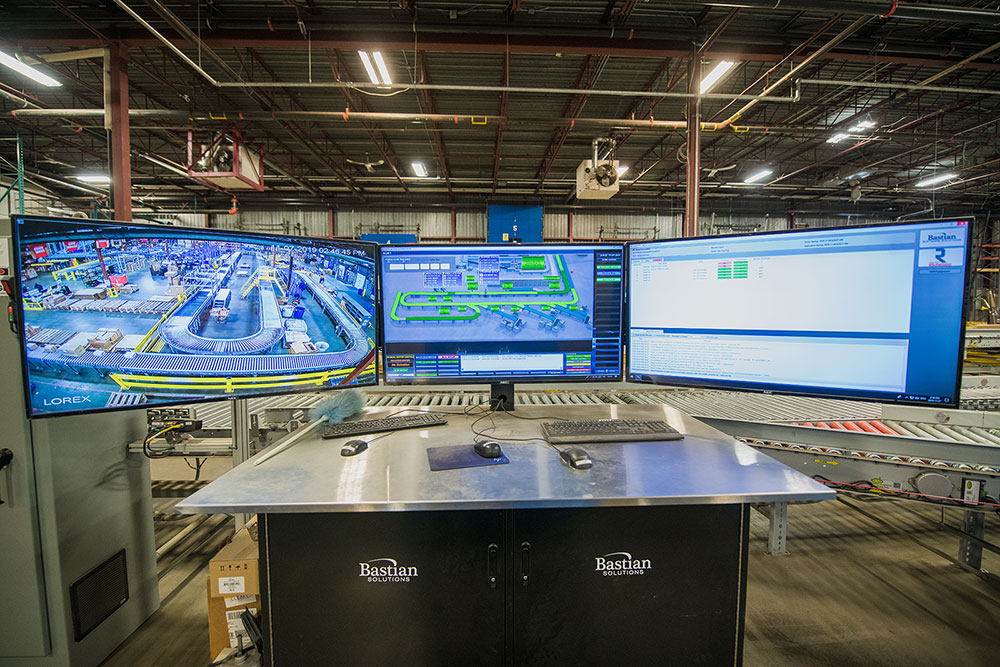
The Whole Picture: Full Warehouse Scope Needed for Effective WES Integration
John Young | 8 May 2024
It’s easy to think of a WES (warehouse execution system) as a “plug-and-play” software solution for islands of automation within a larger overall warehouse system. Just take orders in from the WMS (warehouse management system) or host system, run some logic to sequence those orders in an optimal way and ensure those orders are picked at the right time and place to be shipped on-time.
While, at a high level, this essential functionality is at the core of a WES, operations in all other areas of the warehouse must be understood to guarantee a successful implementation and optimize all interconnected processes at a specific site.
Visibility on an Operational Level
A one-size-fits-all approach to intralogistics software won’t produce a solution that creates immediate efficiencies or adapts to future business needs. To mitigate that risk, warehouse software providers need to have a clear understanding of tasks and processes that make up the day-to-day operations. There are three main operational areas that you’ll want to focus on: inbound, inventory maintenance and picking tasks.
Inbound
Inbound operations are often some of the most overlooked when designing requirements for a WES. After all, the purpose of the system is typically to get goods out in an efficient and timely manner, right? Getting goods in should be straightforward. Perhaps unexpectedly, inbound strategy can have huge effects on storage utilization, labor cost and picking efficiency in both the automation and other areas of the operation.
The main factor that must be considered to define inbound requirements for the WES is the arrival strategy of goods to the automation. Below are some examples and proven solutions for those examples:
- Single-container-size pallets arriving at automation induction ports:
- Typically, the operator decides which automation bin size/configuration to putaway to and the automation continuously brings bins of that size to the operator. This process is very fast and effective if a single case of product fills a certain location size well.
- Depending on how goods are received, this strategy could require additional processing in the WMS to create pallets of similar size cases from reserve storage. This processing needs to be included when considering labor costs in ROI calculations, as well as when considering space for an additional inbound staging area.
- Container routing to automation ports:
- If the application calls for inducting product straight from receiving into the automation, routing containers to certain ports by size may be a good option. Each port can be assigned to a certain location size and putaways can happen very quickly.
- This solution involves more capital expenditure up-front for conveyor and WES routing logic but will likely save on labor in the long run.
- Inventory top-off:
- Depending on the automation, topping product off into a location that already contains some of that product may require additional processing of inbound orders. Typically, this involves building carts of inbound orders in advance so the automation can prepare optimal locations to be brought to induction ports ahead of time.
- This solution is great for storage density but does not make sense for systems that require lot segregation or have limited space for cart staging. This solution also works quite well for returns, as returns are usually low-quantity and should not take up an entire location in the automation.
Inventory Maintenance
Inventory maintenance is vital to the success of any warehouse. This means the WES and WMS must always be on the same page about the quantity of product in automation. There are many different levels to which this synchronization must be checked depending on countries’ laws and companies’ policies. Below are a few examples of how a business’ inventory maintenance requirements can affect automation:
- Frequent cycle counting:
- If all products or locations in a warehouse must be counted multiple times per year, it can have a large effect on the sizing and labor required to run automation. This is especially true if cycle counting must occur during normal picking and induction hours, based on shift schedule.
- Manager re-counts:
- If higher-level employees must confirm any discrepancies in counts performed by operators, it must be considered that these employees may be taken away from other areas of the warehouse operation to perform these tasks at any given moment.
- Cycle counting reserved for certain personnel:
- If there is an inventory team that is responsible for all cycle counting, it must be taken into consideration that other users cannot be granted access to cycle counting functionality. There also must be a strategy for these personnel to split time between automation and other inventory areas.
Picking
There are many variations of picking requirements in automation that depend greatly on downstream processes in the warehouse. Some include:
- Consolidation from many picking areas:
- If an order may be picked partially from automation and partially from elsewhere in the facility, the WES will need instructions to route that order to a consolidation area. If this is done via conveyor, the WES may only require fairly simple routing logic. However, if orders are picked to carts or otherwise manually taken to downstream areas, the WES must know to only pick orders in a batch that share a next destination so that only orders that need combining arrive at consolidation.
- Order/customer categories:
- If different categories of orders (ecommerce, retail, etc.) must be processed differently (different packaging, container size, downstream processes), then they likely must be picked at different ports from the automation to keep the processes separate.
Successful Software Integration
The situations above are just some of the overall business requirements and warehouse processes that technically exist outside of the automation and WES scope, but directly affect the requirements of the WES nonetheless. With our own proprietary intralogistics software suite, Exacta®, Bastian Solutions has software-centric experience handling complex distribution and fulfillment operations across many different industries.
As an independent warehouse system integrator, our expertise spans across the entire warehouse ranging from receiving to outbound operations. Reach out to one of our system experts today to discuss your software and automation needs today.
John is a Logistics Consultant at Bastian Solutions’ software division based in Louisville, Kentucky. He received his B.S. in Mechanical Engineering and M.S. in Business Administration from the University of Kentucky. John works to design software for highly automated systems including those with goods-to-person technology, conveyor routing, sortation, and more.
Comments
No comments have been posted to this Blog Post
Leave a Reply
Your email address will not be published.
Comment
Thank you for your comment.