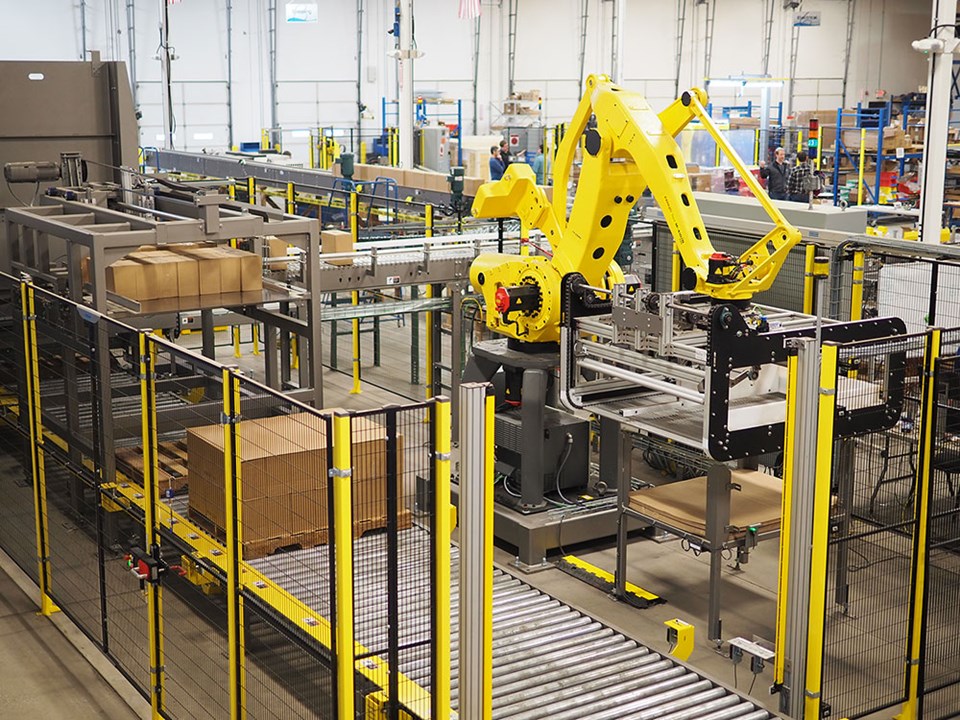
The Ins and Outs of Automated Inbound Palletizing
Mitch Stevens | 30 August 2023
For many distribution centers, unloading trailers and placing inbound product on pallets can be very labor-intensive. There are often hundreds to thousands of boxes in each trailer and these boxes can be large, heavy and hard to reach meaning most reaching, lifting and moving of boxes is done manually. Additionally, the environment inside the trailer can range from cold to extremely hot making it, at times, particularly uncomfortable. As a whole, finding and keeping labor for this essential work often presents a problem. Introducing the right automation to your palletizing operations can address labor availability challenges while also improving margins, throughput and operational flexibility.
Automating Inbound Material Handling at Every Step
Let’s walk through a typical inbounding scenario to pinpoint where material handling technologies can augment to create efficiencies in process flow and also address common operational challenges like labor availability, ergonomic concerns, safety, throughput and flexibility.
Receiving
In the inbound process, first, we begin with conveying the product out of the trailer. This can be done by utilizing a flexible extendable conveyor allows operators to unload the product from the trailer and move it to the dock area. This can be coupled with a portable ergonomic platform that assists the operator with product unloading and conveyance.
Palletizing
Once the product is out of the trailer, it needs to be placed onto a pallet. In order to automate the palletizing process, the product size, orientation (narrow side vs. wide side leading) and SKU will all need to be determined.
-
Establishing Product Size and Orientation: This information can be found using a dimensioning system. This system uses a 3D sensor and encoder to determine a product’s size and orientation on the conveyor. Once the product size has been confirmed, the system can then identify which orientation the case is traveling on the conveyor. The product orientation can be important for downstream conveyance and palletizing processes. For instance, if the downstream sortation system requires that cases be narrow side leading, then cases that are wide side leading will need to be rotated 90-degrees prior to the sortation process. This product rotation can be completed with bump-turners or other mechanisms.
-
Identifying and Sorting Product SKUs: Typically for inbound receiving processes, there are a wide range of products and their identifying barcodes can be located on any side of the case. Therefore, in order to scan the barcode, a five or six sided barcode scan tunnel will be required. The cases travel through the scan tunnel, the scanners read the barcode and the SKU is captured. After the product SKU has been identified, the case will need to be sorted by SKU to a robotic palletizing system. The type and scale of the sortation solution will be driven by the unloading throughput (cases per hour) and average number of SKUs per trailer. Trailers with more SKUs will require more divert lanes and possibly more downstream robotic palletizers. The system throughput requirement will also impact which sortation equipment is needed and drive the number of downstream robotic palletizers. Once the product has been sorted by SKU to a divert lane conveyor, the product will transfer into a robotic palletizing cell.
-
Picking and Placing Products: Once at the robotic palletizing system, the robot will pick the product from the conveyor and place it onto the pallet. Depending on the number of SKUs in the trailer and the system throughput, the robotic palletizing system could include one or multiple robots. The robots can be equipped with custom EoATs (end of arm tools) to handle single or multiple cases per robot cycle, as well as accommodate a wide range of product types. The robotic palletizing systems will also include pallet handling equipment such as pallet dispensers, pallet conveyors, sheet placers, and transfer cars.
Labeling, Transportation and Storage
After the robotic palletizing system has completed the pallet build process, the load will transfer out of the robotic cell and to downstream equipment, such as a stretch wrapper. The automated stretch wrapper will apply stretch film about the load. The wrapped load will then exit the wrapper cell and a print & apply labeling system will apply a label to the side(s) of the pallet. The now completed pallet load will be retrieved by a forklift or transported via conveyor to an AS/RS (automated storage and retrieval system) or industrial racking for storage.
A Solution for Long-Term Resiliency
Selecting the appropriate material handling automation can be overwhelming and is only part of the process in futureproofing your manufacturing or distribution facility. A solution for long-term resiliency is created through data-backed designs, thorough testing, seamless integration and quality customer support. Interested in automating your inbound product receiving processes? Reach out to a Bastian Solutions applications engineer today or visit us at Pack Expo Las Vegas, September 11-13 at booth N-10343.
Mitch is a field application engineer for Bastian Solutions' robotics division. He has Bachelor of Science degree in mechanical engineering from the University of Illinois. As an application engineer, he helps Bastian Solutions’ customers find the right robotic solution for a variety of applications, some of which include palletizing, machine tending, packaging and assembly.
Comments
No comments have been posted to this Blog Post
Leave a Reply
Your email address will not be published.
Comment
Thank you for your comment.