The Most Important Factors of a Robot in a Machine Tending Application
Jason Nowak | 16 June 2015
When trying to figure out what robot fits best into a machine tending application, it is important to look at a number of criteria and weigh the pros and cons of each to determine which one is the best fit.
Robots are extremely precise machines, capable of placing parts in locations within -.005 mm or better. This precision, however, is largely dependent on the reach and payload capabilities of the robot. For instance, typically as the payload or the reach of the robot goes up, the repeatability goes down. This is important to understand because the target of the machine being tended (usually the chuck), and the amount of clearance the part has within the chuck, will dictate how accurately the part must be placed.
Machine tending robot specifications
Every robot manufacturer has features and benefits that they will claim make their robot better than the competition's, but there are a number of criteria that are factual and printed in every robot’s specifications so we’ll focus on those. First, let’s define a few terms, and then we’ll discuss how each one is important in this application.
- Accuracy - This is the robot’s ability to return to a specific XYZ coordinate in space - a certain distance. For instance, if you are throwing a dart at a bull’s-eye. Your accuracy is how close to the center of the bull’s-eye you get.
- Repeatability -The robot’s ability to return to a specific XYZ coordinate in space - a certain distance, time and time again. In this case, if you are trying to hit a bull’s-eye with a dart, your repeatability is how often you hit the bull’s-eye compared to the total number of tries you make. The more times you hit it, the higher your repeatability.
- Accuracy and repeatability are many times confused or interchanged. However, they have different meanings, and thus variously affect how a robot does its job depending on which is more important for the specific application.
- Speed - This is how fast a robot can move from point A to point B.
- Cycle time - This is how fast a robot completes a single task. This is usually picking a part, placing it, and returning to the first point.
- Payload - The amount of weight a robot can handle without slowing down or damaging the robot. Normally, this weight is measured at the wrist of the arm.
- Reach - This is how far a robot can reach in a horizontal direction. Usually, this is a radius measured from the center of the base of the robot.
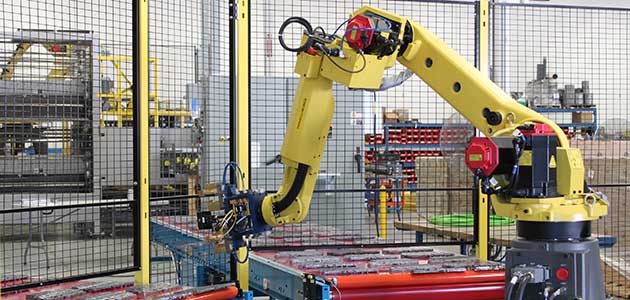
So how do all of these factors affect a machine tending application?
That all depends on what is most important in the application because there are tradeoffs. If you increase any one of the factors mentioned above, this will have an opposite effect on all the others. For instance, if you increase speed, you reduce cycle time. This may also reduce accuracy, repeatability, etc. This might be fine for the application, or it might not be, and it all depends on what the end goal is. To give a real world example of how this all works together, let’s say a robot has the following specifications:
- Reach of 717 mm
- Payload of 7kg
- Repeatability of -.02mm
- Accuracy of 100%
- Cycle time of 10 seconds.
The part we are trying to load into the machine tool has a diameter of 15mm, and the chuck of the machine is 16mm in diameter. Let’s also assume that we have a high volume of parts to machine. In general, that will mean we want to get a finished part out of the machine, and a new part into it as soon as possible. Therefore, increasing speed to the robot’s maximum capability would be desirable. Because the repeatability is -.02mm at an accuracy of 100%, we should have no problem going at the maximum speed the robot can achieve because we have plenty of clearance between the size of the part and the chuck.
If the chuck was smaller, say 15.01mm, then we would want to go with a robot with a high repeatability, and most likely, it would have a slower cycle time. When designing a system, it is very important to have all of these aspects well-defined. It is also very important for the SolidWorks models to be accurate. The robot will be programmed to go to a specific location taking into account cycle time requirements, payload, reach, repeatability, and accuracy. If the models aren’t accurate, then one or more of the robot properties will be adversely affected because the robot will be specified in order to maximize the number of parts produced.
At Bastian Solutions, we incorporate creative designs coupled with the optimum advanced technologies to arrive at a robust machine tending solution that exceeds our customers’ expectations.
Have you designed or implemented a machine tending robot system? What aspects do you find to be most critical?
Jason is a Bastian Solutions Senior Consultant based out of St. Louis, Missouri. He has a Bachelor of Science in Mechanical Engineering from Missouri S&T and an MBA from St. Louis University. Jason has been providing manufacturing and distribution design and integration leadership across various industries for Bastian Solutions’ clients for over 15 years, helping clients develop strategic initiatives and lead successful system implementations.
Comments
jenniferwilliam says:
8/28/2018 10:09 AM
Wah!! it makes our life very easy.
Leave a Reply
Your email address will not be published.
Comment
Thank you for your comment.