The $1.3 Trillion Benefit of Order and System Visibility
Sheila Dooley | 16 April 2015
Warehouse control systems and warehouse execution systems provide real-time visibility into order fulfillment processes, improving speed and accuracy of equipment and ensuring great customer service.
$1.3 trillion… Globally in 2014, that’s how much money consumers spent shopping online. Although especially busy during the holidays, e-commerce retailers are growing increasingly busy throughout the year. Shipping deadlines are tighter, and customer expectations are at an all-time high. As pressure mounts, retailers are depending on automated facilities with material handling equipment for efficient processing of large volumes of orders. But aside from the equipment, software is taking center stage for ensuring order deadlines are met.
A flexible and easy to use warehouse control system (WCS) or a warehouse execution system (WES) with multiple tools is essential for success. These systems have the ability to assist with the tracking and visibility of orders, and they provide statistics anywhere from a scanner read rate to the number of orders shipped during a specific working shift. In addition, these tools assist in immediate resolution of system issues, which is a critical factor in system uptime and throughput. Below are examples of WES and WCS solutions implemented by Bastian Solutions’ customers and highlights of what these systems can do to improve order capacity:
- Real time, up-to-the-second view into orders on the floor and those shipped to the customer
- Ability to create and quickly export to Microsoft Excel or PDF views for processing data metrics
- Immediate knowledge of equipment exceptions and issues as they happen, quickly resolving motor faults, jams and e-stop pulls
- Daily and weekly tracking of statistics and trends
- Color-coded, 3-D graphical views of equipment by area to quickly identify problems and status changes
- Remote visibility on a phone, tablet or PC, meaning managers and directors can spend time at home and still keep tabs on multiple shift operations
In a nutshell, with the right warehouse control system or warehouse execution system, a company has greater visibility of its entire operation. Here are three examples of real-time dashboards you can use to monitor your operation and ensure peak uptime.
Human Machine Interface (HMI)
The first is an example of our Human Machine Interface (HMI). These screens allow operators to see where jams or bottlenecks are occurring within their order fulfillment system. Green means everything is running smoothly. Yellow equals slow, and red means there is a jam.
Exacta Portal Reports
Depending on your equipment, facility areas and operators, there are a number of reports that can be generated from within your warehouse execution system. This includes operator cycle time, putaways per aisle, open picks, total lines picked per work area, etc.
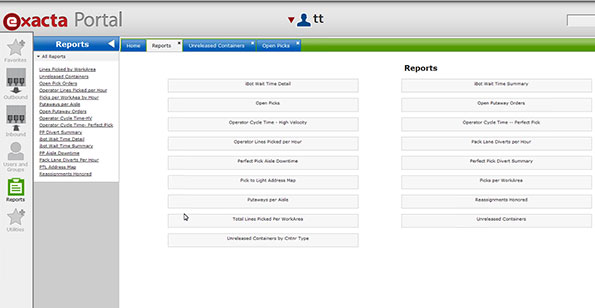
Custom Exacta Reports
This report is an example of how operators can view throughput during an entire shift to see how many orders have dropped and how many have been picked and completed. This helps shift managers monitor throughput levels as they compare to shift goals and overall performance.
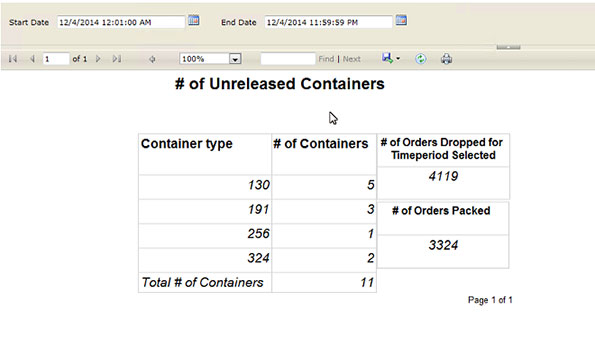
Automated Order Routing (AOR)
This application is at the core of system routing and can also be an incredibly resourceful tool. You have the ability to select which scanner(s) from which to read logs, and read rates can be found and cleared every day without re-starting the AOR program. You have the option to “Scroll on New Message,” “Remove Messages,” etc.
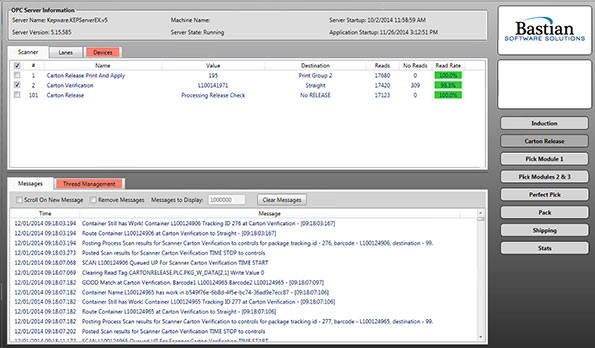
With the right supply chain software, there are many ways to ensure orders are fulfilled in an efficient manner, while giving you complete system visibility. This not only helps with throughput, but more importantly, ensures customer orders are accurately fulfilled and delivered on time.
As a Business Analyst for Bastian Solutions, Sheila works as part of the sales team for the software division working with prospects and customers to understand their software requirements. Prior to joining Bastian, Sheila worked as a project manager for a consulting firm helping customers in a variety of industries with warehouse management system requirements, documentation and implementation.
Comments
No comments have been posted to this Blog Post
Leave a Reply
Your email address will not be published.
Comment
Thank you for your comment.