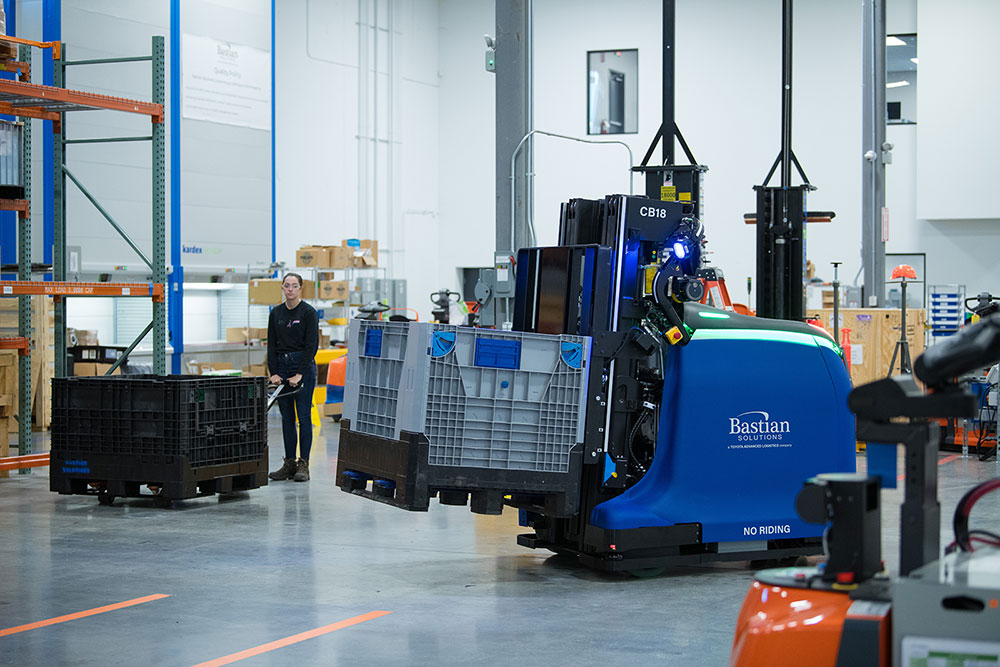
Efficiency and Safety: Navigation in Industrial AVs
Kyle McMillin| 13 March 2024
Within the realm of industrial vehicle automation, the terms “dynamic path planning” and “obstacle avoidance” have recently generated buzz. On the surface, the idea of an AV (autonomous vehicle) having the capability to independently navigate around unforeseen obstacles appears to be a valuable feature. And, make no mistake, there are certainly specific applications where that feature can be beneficial. This blog post will expand on the other navigation methods and why AV OEMs (original equipment manufacturers) make the deliberate choice to use them.
Understanding the Alphabet Soup
Before delving into these insights, let's lay down some basic definitions to ensure a collective understanding.
The ANSI (American National Standards Institute) distinguishes between AGVs and AMRs through the following definitions:
- AGV (automated guided vehicle): “An AGV moves through an environment by following predefined guide paths — either virtual or physical — and using collision avoidance (stopping and waiting in case of a blockage).”
- AMR (Autonomous Mobile Robot): “[AMRs] traverse the specified operating environment by detecting obstacles using sensors and adjusting paths by computing an obstacle-free path through free space, rather than using a pre-defined path.”
Typically, AVs perform missions to get from point A to point B using the following methods:
- Path Planning: The AV follows a predefined route. If the assigned route gets blocked by an object, the vehicle will wait until that object is removed until it resumes the route.
- Obstacle Avoidance: The AV follows a predefined route. If the assigned route gets blocked by an object, the vehicle will make its own “intelligent” decision to navigate around the object and return to its preassigned mission as quickly as safely possible.
- Dynamic Path Planning: AV makes its own “intelligent” decisions on the most efficient way to get from point A to point B. The path and route timing can be different every time based on changing environmental factors.
Navigation in Industrial Operations
When assessing whether obstacle avoidance or dynamic planning is appropriate, the environment becomes a significant factor. For instance, universities across the country have integrated AVs for delivering mobile food orders to students on campus. These vehicles operate in an exceptionally dynamic environment with students in motion, unpredictable food truck locations, bicycles and more. In such scenarios, a purely path-following vehicle would struggle to reach its final destination due to the constant changes in the environment, making dynamic path planning or obstacle avoidance a perfect fit.
How does this example differ when applied to manufacturing and distribution centers, and when does it make sense to employ a path-following vehicle? While the reasons are numerous, these facilities are typically intricately designed to maximize efficiency and minimize variability. The vast scale and substantial investment in these facilities necessitate the efficient utilization of every square foot.
Considerations for Utilizing AVs in Material Handling
Below are a few factors to consider when looking at path-following and dynamic-planning vehicles in industrial environments.
- Safety
Safety should be the paramount consideration for every corporation when selecting an automation form factor. In the case of a vehicle utilizing obstacle avoidance or dynamic path planning, the path of the AV can become unpredictable. This lack of consistency introduces uncertainty for employees. When the system is fully dynamic, how can team members anticipate the vehicle's trajectory?
AVs have the capacity to transport payloads ranging from small to extremely large, and a dynamically planning system may deviate from its regular route based on 'intelligent' decisions. This unpredictability can make team members uncomfortable, potentially escalating the risk of safety incidents. On the contrary, path-following AVs offer a solution by consistently following the same path every time. Over a short period, operators become familiar with the AV's predictable trajectory, creating a safe and highly predictable system.
- Consistency
Throughput and cycle time stand as pivotal concerns in the industrial and warehousing domains, where production lines meticulously adhere to exact cycle times for precise process alignment and slow fulfillment rates can negatively impact a company’s reputation with customers. Deviations from these cycle times can result in overcapacity, leading to efficiency challenges or the costly scenario of line downtime, incurring tens to hundreds of thousands of dollars per hour in lost revenue. When an AV maneuvers around obstacles or dynamically plans its own path, the time required to travel from point A to point B exhibits significant variability. This fluctuation introduces the risk of timely deliveries in one mission while opting for a less-than-optimal route in another, resulting in delays.
In contrast, a path-following AV offers consistent, efficient and reliable travel times from point A to point B. Illustrating this, BlueBotics' CEO, Dr. Nicolas Tomatis, shares an example:
“Consider the feedback we received recently from one AGV maker. One of its customers, a tire manufacturer, previously operated a fleet of 37 [AMRs], all of which used obstacle avoidance. When the company decided to retrofit these vehicles however, it went with pure path-following ANT® navigation in tandem with our ANT® server fleet management software. The tire firm actually installed seven fewer AGVs in all. But the 30 it now uses have proven to be 10% more productive than its previous 37. When it comes to overall efficiency, that’s the path following difference.”
BlueBotics is a globally recognized company that provides brand-agnostic natural features navigation technology, called ANT (Autonomous Navigation Technology), for the development of AGVs and AMRs. They emphasize that both path-following and dynamic path planning AVs have distinct applications in the market when applied correctly.
- Organizational Control
When installing any automation technology into a facility, it is an integrator’s responsibility to assist the end user’s team members in designing organizational control around the automation to optimize the beneficial impact. Without proper organizational control, automation will instead highlight inefficiencies and operations without proper process. Autonomous vehicles are no different in this regard. If the technology advertises the ability to navigate in a purely chaotic environment, what kind of affect would that have on processes going forward?
The implication is that automation can overcome sloppy processes, which of course can be a slippery slope. While you may lose some initial efficiency with a path-following AV system if an object is placed in its path, operators will quickly learn to follow process and keep the route clear to maximize the system effectiveness; in turn making their processes run smoother. This sentiment is again reinforced by Dr. Tomatis, “Even with perfect obstacle avoidance, if your AGVs or AMRs have to move around objects, that slows down their progress compared to path followers, where the staff is trained to keep routes free.”
Expert AV Consultation and Planning
The robust landscape of industrial vehicle automation presents choices between obstacle avoidance, dynamic path planning and the path-following approach. The intricacies of each method find their relevance in diverse environments, where safety, consistency and organizational control play pivotal roles.
Navigating the evolving terrain of autonomous vehicles can be difficult, and that’s where the expertise and experience of a systems integrator can be invaluable. Bastian Solutions, with our own AV manufacturing group, can help provide a solution that delivers reliable and efficient outcomes. Once our experts understand the specific demands of your environment, we’ll find the perfect balance of adaptability and structure that meets your current and future needs.
Speak to myself or one of our engineers at our MODEX, March 11-14 in Atlanta, Georgia. Our booth, B5619, will feature autonomous vehicles as well as several other material handling technologies. See you there!
Kyle McMillin is an Application Engineer at Bastian Solutions’ Autonomous Vehicles Group, based in Georgetown, KY. He has Bachelor of Science degrees in Supply Chain Management-Engineering and Finance from Auburn University. As an Application Engineer, Kyle works with clients to analyze, design, and implement autonomous vehicle systems.
Comments
No comments have been posted to this Blog Post
Leave a Reply
Your email address will not be published.
Comment
Thank you for your comment.